L’auto elettrica e ibrida rappresentano un’evoluzione del trasporto coerente con la necessità di uno sviluppo sostenibile. Per appianare le criticità che ne rallentano la diffusione non mancano proposte organiche e intelligentemente strutturate. Una di queste è il progetto CarE-Service – finanziato dal programma quadro dell’Unione europea per la ricerca e l’innovazione Horizon 2020 – che aggrega quindici tra aziende e centri di ricerca internazionali, impegnati nella creazione di una piattaforma che coordina tutti gli “anelli” di una supply chain per certi aspetti ancora inedita. A poco meno di un anno dalla deadline si è svolto il primo Exploitation Event di CarE-Service, promosso dal partner FCA (Fiat Chrysler Automobiles) per presentare i risultati preliminari a imprese e professionisti, potenziali futuri utenti delle soluzioni sviluppate. Scopriamo di cosa si tratta.
Un modello di business sostenibile tracciato e testato
«Un costo ancora elevato, perplessità legate alla facilità di ricarica, all’autonomia e ad un’esperienza di guida poco convincente frenano la diffusione della mobilità elettrica in Europa» sostiene Giacomo Copani, ricercatore presso STIIMA-CNR e coordinatore del progetto. «Una soluzione per colmare questi gap è rappresentata dallo sviluppo di modelli di business circolari innovativi, integrabili ai servizi offerti dalle società di car sharing, che puntino sia a soddisfare esigenze di fruizione personalizzate, sia a rendere più sostenibili i costi per l’utente attraverso interventi mirati sulla manutenzione, attuabili attraverso una gestione “virtuosa” del fine vita dei veicoli. Non si tratta quindi solo di sostenibilità economica e sociale, ma anche ambientale».
La logica che muove il progetto CarE-Service è la creazione di un marketplace dove far incontrare la domanda e l’offerta di parti di veicoli in rottamazione, che possono essere riutilizzate su auto ancora circolanti, diventando quindi dei ricambi ancora pienamente utilizzabili. Il flusso di questi materiali è gestito da una piattaforma ICT appositamente sviluppata, che supporta il disassemblaggio e il testing dei pezzi, ma anche la logistica per la spedizione. Peculiarità del progetto è l’impiego di attrezzature mobili, connesse attraverso il cloud alla piattaforma, equipaggiate con sistemi robotici per lo smontaggio di componenti chiave, la verifica della funzionalità e la certificazione finalizzata all’utilizzo da parte di officine di manutenzione o altre realtà appartenenti alla catena del valore CarE-Service. Il loop riportato nella figura 1 esemplifica il concept e la logica del progetto europeo.
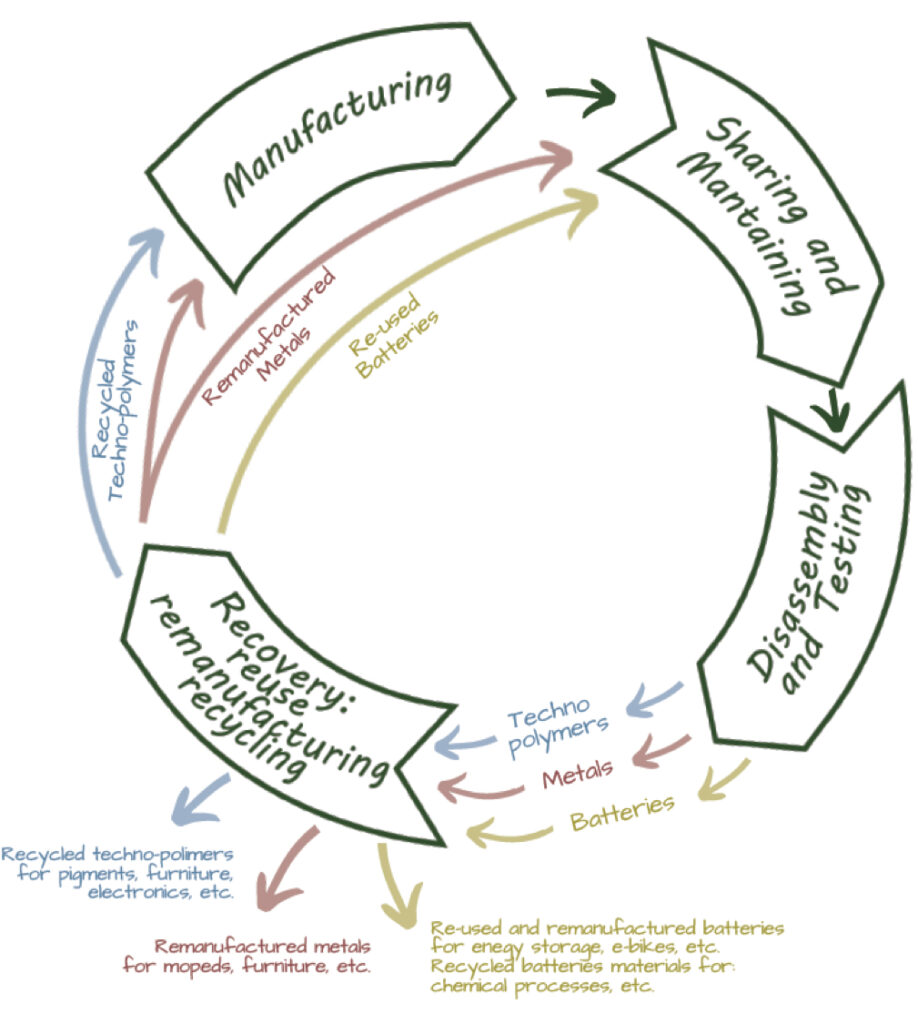
End of life dei componenti
Ma dove finisce tutto quello che non può essere immediatamente riutilizzato? Le batterie così come i componenti in metallo e i tecnopolimeri vengono messi in vendita nel marketplace digitale e acquistati da aziende che li trasformano, facendoli entrare in tre distinte catene del valore basate su recupero, riuso e riciclo. Partner del progetto attivo nell’economia circolare dei tecnopolimeri è RadiciGroup, produttore di poliammidi – nonché fornitore di FCA e di altre realtà produttive del mondo auto – che da molti anni propone gradi ottenuti da scarti post industriali. «La partecipazione al programma ci ha aperto nuovi orizzonti, facendoci comprendere che esistono molte fonti di approvvigionamento di materia prima post consumo oggi ancora poco sfruttate, compresa quella dell’auto» spiega Riccardo Galeazzi, CAE Engineer, Post consumer Product Manager e responsabile del progetto CarE-Service in RadiciGroup. «Per l’auto elettrica l’obiettivo dell’alleggerimento è ancora più importante rispetto alle auto tradizionali e rappresenta una possibilità per aumentarne l’autonomia. Quindi serviranno materiali leggeri da un lato, ma con proprietà elevate tali da permettere una sostituzione efficiente dei metalli. Il nostro impegno nell’ambito del progetto punta proprio in questa direzione» sottolinea. «La procedura sviluppata – oggi in scala pilota – mira a conseguire tre aspetti fondamentali: controllare e limitare la variabilità delle proprietà del materiale riciclato prodotto con delle materie prime post consumo, preservarne le prestazioni o cercare di migliorarle, valutare la sostenibilità del processo di riciclo in termini economici e di impatto ambientale».
La seconda vita delle poliammidi
Sia per motivi di tradizione del Gruppo, sia per il minor impatto ambientale, la procedura proposta si basa sul riciclo meccanico. «Dal momento che la produzione di un compound da post consumo di qualità richiede un’accurata selezione della materia prima di partenza, nella prima fase del progetto ci siamo concentrati soprattutto sul disassemblaggio delle parti e sui pretrattamenti dei componenti ottenuti» continua Galeazzi. L’operazione, che si è rivelata fondamentale per individuare i pezzi economicamente più vantaggiosi dal punto di vista del riciclo, considera tre importanti variabili: la facilità di smontaggio, la quantità di tecnopolimeri presenti e la loro purezza. Si è quindi effettuato lo screening su diverse parti, come serbatoi del radiatore, airbag esplosi (figura 2), supporti del cambio, ventole di raffreddamento, copriruota (figura 3), convogliatori dell’aria, coperture del motore e delle valvole, maniglie delle portiere e tergicristalli posteriori.
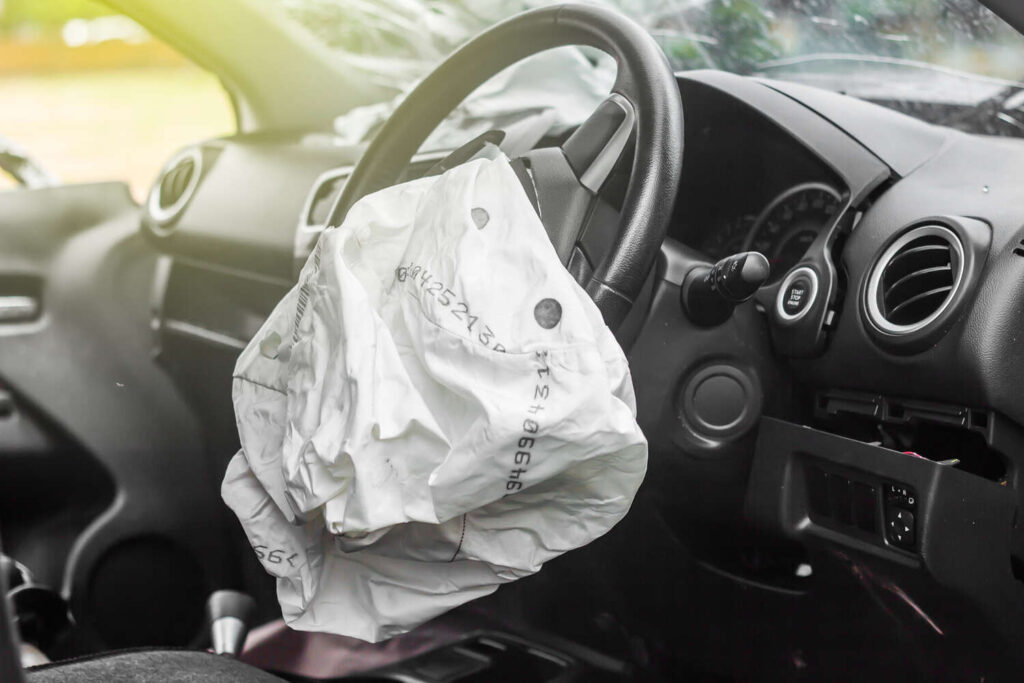
Per ciascuna di queste tipologie sono state raccolte quantità pilota di materiale, dalle quali sono stati separati i componenti in plastica e quelli non adatti al riciclo (metalli e altri inquinanti). I copriruota, gli airbag, le maniglie delle portiere e i tergicristalli posteriori si sono rivelati i più adeguati. «Dagli scarti di copriruota e airbag si è ottenuta una poliammide 6.6 che abbiamo utilizzato per mettere a punto la procedura di riciclo, mentre le resine a base poliestere (PET e PBT) ricavate dalle maniglie e dai tergicristalli sono servite per validare la metodologia di riciclo» spiega Galeazzi. «I copriruota sono stati lavati con detergente sgrassante e acqua calda ad alta pressione, al contrario di tutte le altre parti che, visto il grado di pulizia accettabile, non sono state sottoposte ad alcun trattamento. Al termine dell’operazione, i materiali sono stati macinati e quindi analizzati prima di essere impiegati nella formulazione di polimeri da post consumo».
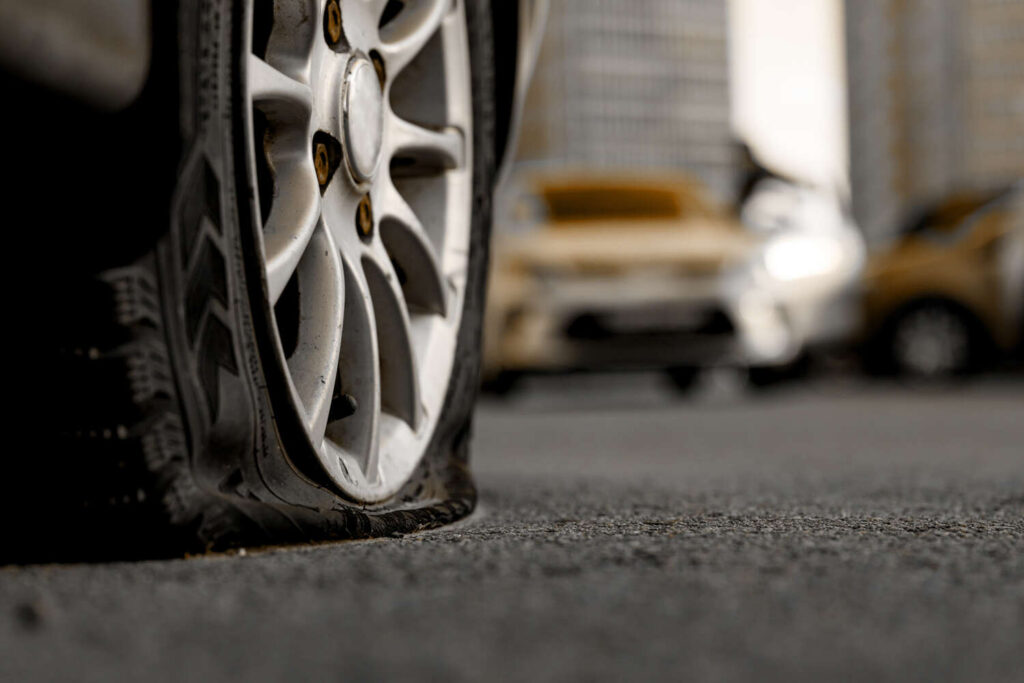
Mantenere alte le prestazioni
«Durante la formulazione del compound da post consumo abbiamo osservato un decadimento delle proprietà meccaniche rispetto agli omologhi ottenuti da polimeri vergini, di entità anche molto variabile in relazione al componente di origine della materia prima» continua Galeazzi. «Per limitare il più possibile la variabilità delle proprietà del materiale prodotto e preservarne le performance è stato necessario effettuare un accurato tuning della formulazione. I test effettuati sui materiali “scouting”, contenenti percentuali differenti di poliammide proveniente da copriruota e airbag – sebbene sia evidente un lieve decadimento delle proprietà rispetto ai materiali di riferimento vergini e post industriali – hanno mostrato risultati positivi e sostanzialmente uniformi in termini di prestazioni meccaniche (figura 4)».
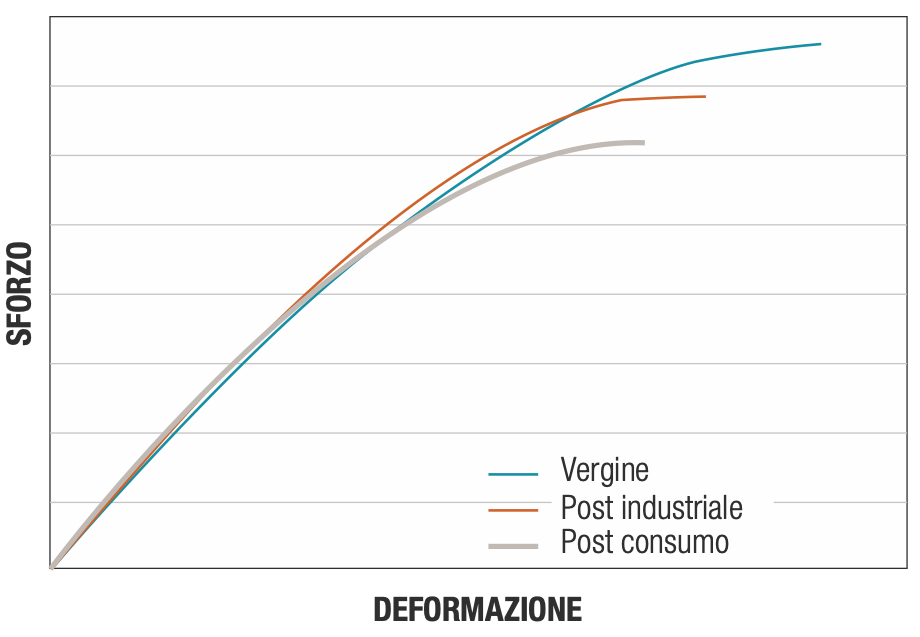
Design for recycling per chiudere il cerchio
«Dagli airbag esplosi abbiamo ricavato una poliammide 6.6 caricata con il 30% di fibre in vetro caratterizzata da una resistenza a trazione leggermente superiore rispetto ai gradi di riferimento post industriali, ma da una resistenza all’impatto leggermente inferiore» continua Galeazzi. «Le resine da post consumo ricavate dai copriruota mostrano un profilo nel complesso positivo, ma meno prestazionale per resistenza a trazione e allungamento a rottura. La presenza di contaminanti non eliminabili, che restano visibili come piccole inclusioni nel materiale riciclato, tende infatti a compromettere l’impiego del compound in applicazioni dove sono presenti carichi meccanici elevati. Da questa osservazione emerge che per rendere il riciclo un processo pienamente attuabile è davvero urgente l’adozione dei criteri di design for disassembling e recycling, purtroppo oggi ancora scarsamente diffusi» sottolinea.
Il ruolo della progettazione appare decisivo anche valutando il processo di riciclo in termini di sostenibilità ambientale, tema sul quale è intervenuta Susanna Caprotti, responsabile Environmental Product Declaration (EPD) di RadiciGroup. «Il materiale da scarti post consumo di per sé è “environmental free”, ovvero non gravato dall’impronta ambientale del materiale vergine» precisa. «Lo studio di Life Cycle Assessment (LCA) di un compound da post consumo, dunque, prende il via dalla fase di smontaggio e separazione: più è agile la procedura, minore è il suo impatto ambientale e maggiore la possibilità di riutilizzo in un’applicazione tecnica».
Prevedere il comportamento
L’intrinseca perdita di prestazioni e la loro variabilità nei polimeri da post consumo soggetti alle dure condizioni d’uso dei componenti auto – come i carichi meccanici, l’azione degli UV, l’aggressione chimica e l’usura – potrebbero far ritenere inevitabile il loro impiego in applicazioni di livello inferiore. «In realtà non è così» sostiene Claudio Ghilardi, CAE Engineer presso RadiciGroup. «Gli strumenti di simulazione CAE, infatti, sono una valida possibilità di supporto per gli ingegneri nella scelta del materiale e permettono la valutazione delle modifiche alla geometria del componente (nervature di rinforzo, aumento di spessori, forme diverse) che compensino il decadimento delle proprietà».
Le simulazioni di processo vengono utilizzate al fine di prevedere il comportamento dei materiali durante lo stampaggio a iniezione, quelle strutturali consentono di verificare la resistenza meccanica delle parti stampate. Caratterizzazione meccanica del materiale, geometria del componente, sua discretizzazione, e vincoli di design: da questi input i sistemi CAE forniscono risultati di ampia affidabilità, che sono confrontati con test fisici eseguiti sui medesimi componenti pilota per comprendere se il materiale è indicato per l’utilizzo.
«Nell’ambito del progetto CarE-Service, la poliammide 6.6 caricata con il 30% di fibre in vetro ricavata dal riciclo degli airbag è risultata adatta alla produzione di una cover che protegge il dispositivo di regolazione di una scrivania, costituita da due semi gusci assemblati con una precisione tale da rendere determinante la valutazione dell’entità di deformazioni o ritiri» continua Ghilardi. «Una seconda applicazione alla quale stiamo lavorando è mirata al settore automotive. Non si tratta di un componente di sicurezza perché il compound non eguaglia le prestazioni del materiale vergine, ma è perfettamente adeguato a parti, come il convogliatore dell’aria o altre tipologie di collettori per aerare l’interno dell’abitacolo, che non richiedono grandi prestazioni meccaniche e possono essere efficacemente realizzate con il materiale da post consumo» conclude.