Grande leggerezza, ma anche stabilità dimensionale elevata e ritiro uniforme. Sono alcuni dei vantaggi promessi da MuCell, la tecnologia di stampaggio a espansione già apprezzata nel settore automobilistico per la produzione di componenti sottocofano e di particolari di grandi dimensioni per l’interno della vettura. Oltre ai miglioramenti delle caratteristiche del pezzo, la tecnica ha effetti sostanziali anche sul processo di stampaggio, come una diminuzione del tempo di ciclo fino al 50 per cento, una riduzione della pressione e della temperatura di esercizio: elementi che permettono di operare con macchine a iniezione di tonnellaggio inferiore, quindi economicamente più accessibili e di dimensioni minori, contenendo così il consumo energetico. Tre fattori, questi, determinanti ai fini dell’efficienza del processo produttivo, e che si potranno verificare direttamente a Mecspe.
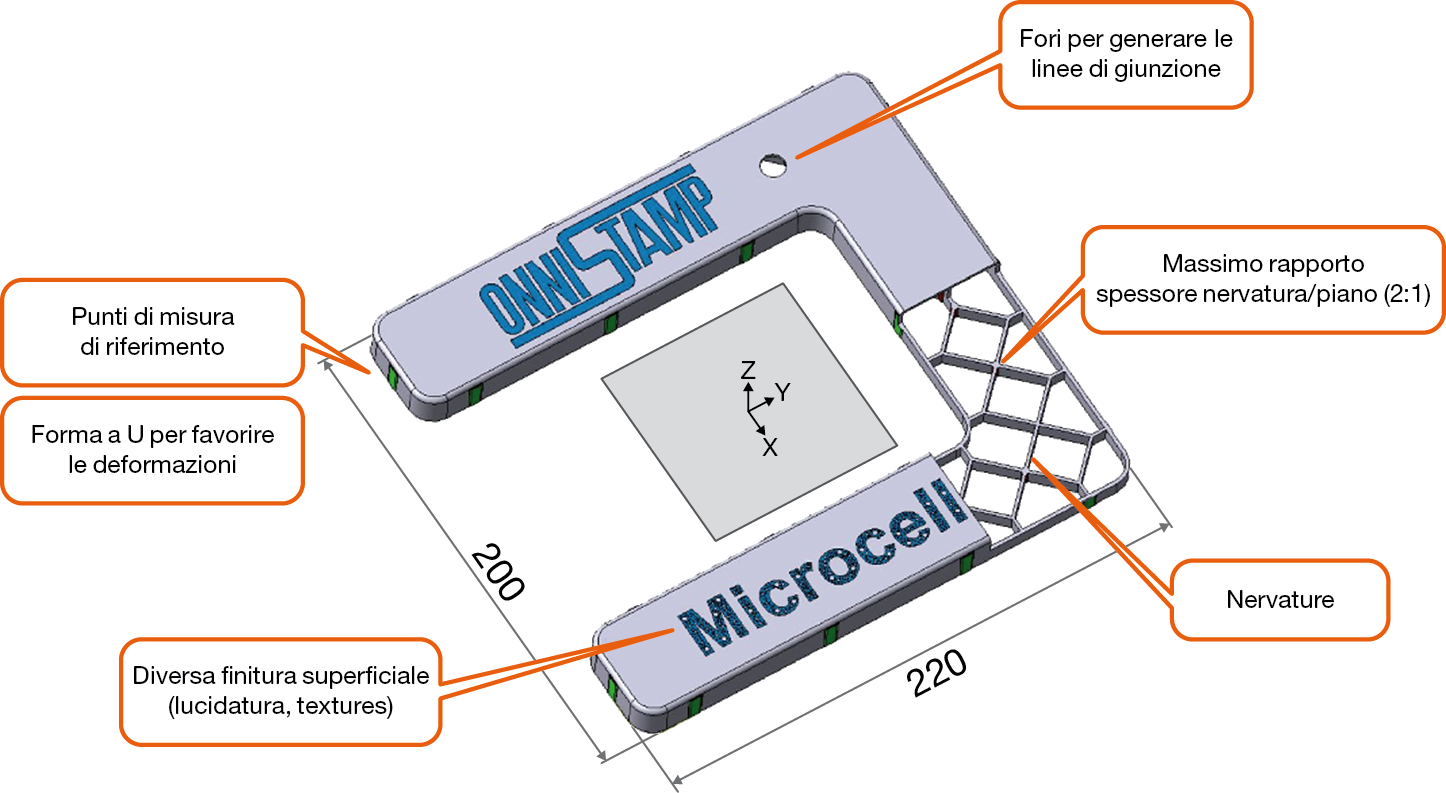
Nello stand E24 (padiglione 6), un pool di aziende (Engel, Frigel, Leonardi, Moldex 3D, Onni-Stamp e Proplast) allestirà un’isola di lavorazione dedicata alla produzione di un componente particolarmente critico dal punto di vista sia della forma, sia della finitura superficiale. Si tratta di un pezzo in ABS nero (Starex HF 0660 di Samsung fornito da Leonardi) a forma di U – quindi soggetto a deformazione –, forato e provvisto di una serie di nervature superficiali, disegnate volutamente con elevato rapporto dello spessore rispetto a quello di parete. Il componente verrà stampato su una pressa ibrida Engel e-victory 440/120 da 120 tonnellate, senza colonne e con piani maggiorati, equipaggiata con cilindro, vite e sistema di controllo integrato specifici per il MuCell. La regolazione della pressione del gas supercritico iniettato (in questo caso azoto) sarà assicurata da una centralina Trexel.
Il pezzo verrà prodotto attraverso uno stampo a un’impronta, progettato e realizzato da Onni-Stamp con canali conformali su entrambi i semistampi, al fine di migliorare l’aspetto superficiale dei componenti stampati attraverso la combinazione dello stampaggio a espansione e della tecnologia di heat and cool. A frenare la diffusione del processo MuCell nella realizzazione di pezzi “a vista” è stata l’estetica. Questo almeno fino a pochi mesi fa, perché i ricercatori Proplast hanno dimostrato che tale ostacolo è superabile unendo le potenzialità delle due tecnologie sopra menzionate. Oltre alla sperimentazione, lo studio condotto dal Consorzio piemontese prevede la simulazione (effettuata con il software Moldex3d) dello stampaggio a espansione.
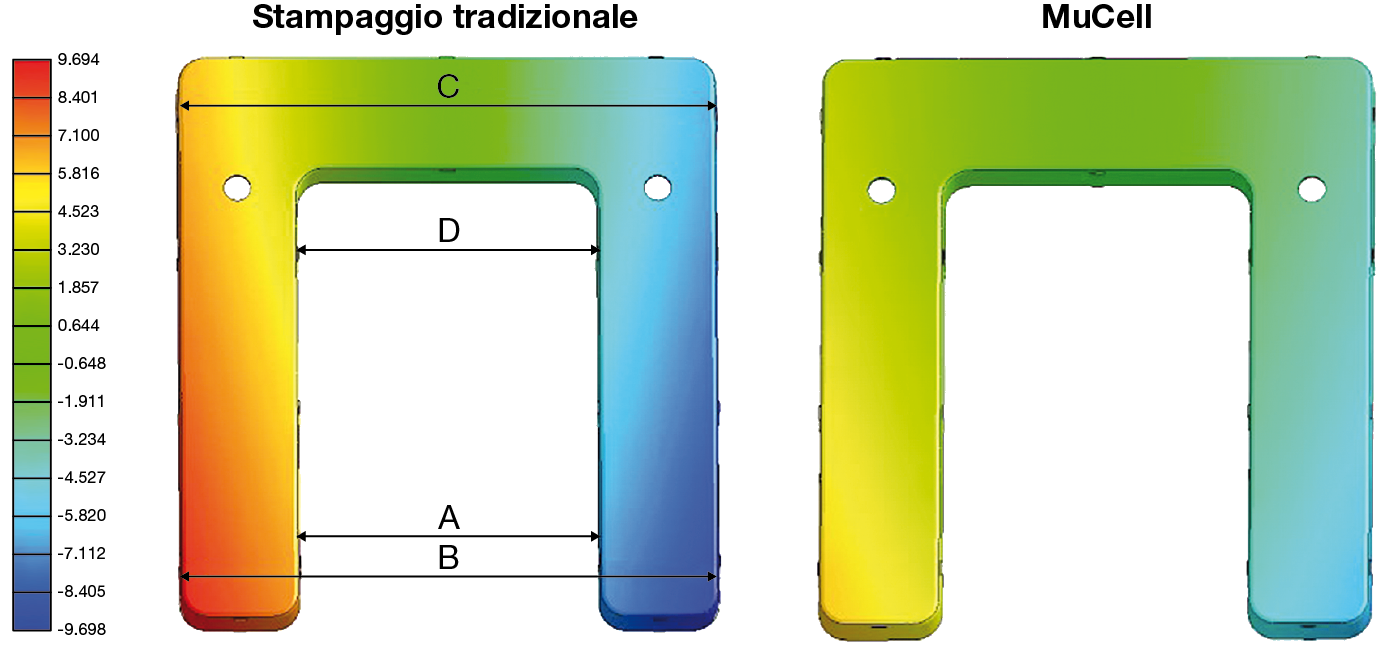
Completano l’impianto presentato in fiera un sistema di termoregolazione a doppia zona di Frigel (modello RAD 80), un alimentatore e un deumidificatore Moretto e un robot Engel viper 12 integrato per la movimentazione dei pezzi.
I dettagli e i risultati del progetto verranno illustrati da Andrea Romeo di Proplast nel corso del workshop “Industrial design: i cinque sensi della plastica”, che si terrà venerdì 28 marzo dalle 10:00 alle 13:00 nella sala B pad.7 della fiera di Parma. Maggiori informazioni e iscrizioni a questo link.