Nella “Strategia europea per la plastica nell’economia circolare” la Commissione europea ha lanciato una sfida al settore, chiedendogli di portare il volume di plastica riciclata introdotta in nuovi manufatti dagli attuali 4-5 milioni di tonnellate l’anno ai 10 milioni di tonnellate entro il 2025. Raggiungere l’obiettivo richiede non solo un impegno volontario da parte delle imprese e un aumento della capacità di trattamento dei rifiuti da raccolta differenziata, ma anche tecnologie di trasformazione più efficienti.
Engel ha deciso di contribuire all’obiettivo proponendo soluzioni per migliorare il processo di stampaggio a iniezione. Lo sforzo è stato riconosciuto da Bloomberg, che ha inserito nella classifica dei 50 leader globali del clima il costruttore di macchine austriaco, l’unico nella sua categoria.
La variabilità della materia prima
Una delle maggiori criticità nella trasformazione dei polimeri rigenerati è legata alla variabilità delle loro caratteristiche, che cambiano in funzione della contaminazione dei rifiuti utilizzati e del processo impiegato per lavorarli. La disomogeneità dei diversi lotti si ripercuote sul processo di stampaggio a iniezione inficiandone la ripetibilità. Engel – in collaborazione con il produttore di impianti per il riciclo Erema – ha dimostrato, attraverso una sperimentazione dedicata, che il problema può essere risolto grazie all’impiego del sistema Engel iQ weight control. La prima serie di prove è stata effettuata con una macchina a iniezione Engel victory 120 equipaggiata con uno stampo per la produzione di provini rettangolari in polipropilene rigenerato, ottenuto da materiali geotessili utilizzati nei cantieri edili, quindi caratterizzati da un’elevata contaminazione. I tessili sono stati lavati, processati e rigranulati mediante gli impianti Erema. Per simulare condizioni realistiche durante l’esecuzione dei cambi lotto, sono state utilizzate quattro diverse combinazioni di tecnologie di riciclo e parametri di processo. I quattro materiali riciclati così ottenuti presentavano indici di scorrimento (melt flow index o MFI) compresi tra 15 e 30 g/10 minuti e caratteristiche differenti, di conseguenza un comportamento diverso in fase di stampaggio.
Rilevamento e compensazione delle differenze
Durante una seconda serie di test sono stati stampati dei manubri da pesistica. Per valutare la ripetibilità del processo e la conseguente qualità del manufatto, particolare attenzione è stata dedicata al riempimento dello stampo e alle proprietà meccaniche del polimero, ad esempio la resistenza agli urti. Come è noto, le caratteristiche meccaniche e la viscosità dipendono dal peso molecolare, pertanto è possibile considerare la variazione di viscosità un indicatore di quella della lunghezza delle catene polimeriche. iQ weight control è in grado di individuare anche le più piccole deviazioni di viscosità rispetto a un valore di riferimento. Il rilevamento (automatico) di una variazione della viscosità diventa quindi un indicatore di una possibile variazione nella distribuzione della lunghezza delle catene polimeriche. Regolando il profilo di iniezione, il punto di commutazione e la curva della pressione di mantenimento, il sistema di assistenza mantiene costante il volume di riempimento anche in presenza di valori variabili di viscosità, impedendo quindi i riempimenti parziali dello stampo. Il riempimento più uniforme contribuisce inoltre a garantire sempre la medesima forza di compressione. I cali di forza provocati dalla diminuzione del peso molecolare della materia prima, infatti, non possono essere compensati mediante il controllo di processo.
iQ weight control: più utile del melt flow index
L’indice di scorrimento (MFI) viene comunemente utilizzato come indicatore della fluidità del fuso, ma questa misura, purtroppo, non tiene conto degli effetti della velocità di taglio sulla viscosità. Le plastiche fuse hanno un comportamento pseudoplastico, quindi la loro viscosità tende a diminuire al crescere della velocità di taglio. Dal momento che, durante lo stampaggio a iniezione, la velocità di taglio risulta sensibilmente più elevata rispetto a quanto misurato in base al MFI, la validità di questo indice in sede di valutazione della fluidità in condizioni di processo risulta perlomeno dubbia. iQ weight control, al contrario, riesce a rilevare le variazioni di viscosità in base alle velocità di taglio che si determinano effettivamente durante il processo, consentendo pertanto misure più precise (figura 1).
Nel corso della sperimentazione è emerso che le misure di MFI effettuate in condizioni di basse velocità di taglio concordavano con quelle ottenute mediante il reometro capillare ad alta pressione (HCR), che indicava una differenza del 23,7% tra i valori di fluidità dei due materiali esaminati. Durante il processo di stampaggio a iniezione iQ weight control, invece, ha calcolato una differenza di viscosità pari a +11,7%, valore confermato dal 12,4% rilevato con l’HCR in presenza della velocità di taglio corretta (figura 1, a sinistra). Se le curve relative alle due viscosità dipendenti dalla velocità di taglio si incrociano, un materiale il cui MFI indichi una scarsa fluidità potrebbe scorrere più agevolmente nelle condizioni di processo reali. Anche in questo caso, iQ weight control fornisce il risultato corretto: -5,4% (figura 1, a destra).
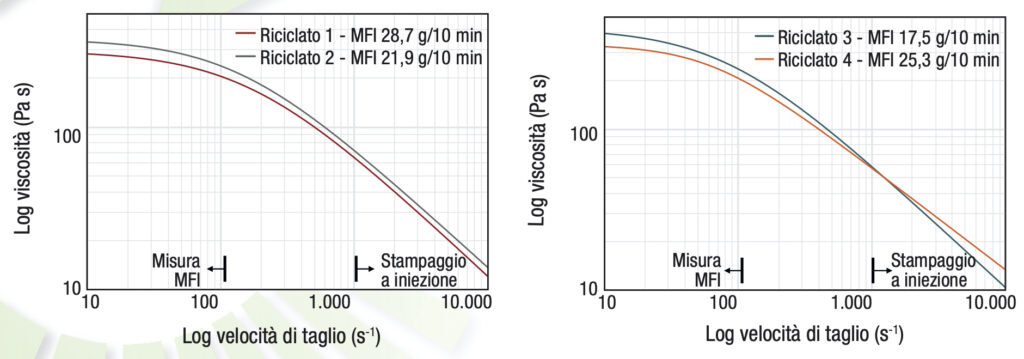
Stampaggio di parti con geometria complessa
Per riuscire a valutare l’attendibilità del software in presenza di geometrie complesse, in un’ulteriore serie di prove è stato utilizzato uno speciale stampo per realizzare un provino dalla struttura ramificata, costituita da pannelli di spessori diversi (figura 2). La struttura presenta uno spessore di 3 millimetri lungo l’elemento centrale, mentre i bracci laterali sono spessi 2, 1 e 0,5 millimetri, con le zone più sottili situate alla fine del canale di adduzione.

Per lo stampaggio dei provini sono stati impiegati due dei quattro materiali rigenerati prodotti da Erema, uno dei quali è stato utilizzato come riferimento (riciclato 1). Al passaggio dal materiale di riferimento al secondo (riciclato 2) è emerso che, senza l’assistenza di iQ weight control, il peso della stampata diminuiva sensibilmente e non risultava più possibile riempire completamente l’impronta (figura 3). Quando è stato attivato iQ weight control, invece, il peso della stampata aumentava fino a raggiungere i valori ottenuti con il materiale di riferimento, consentendo la produzione di manufatti completi e di qualità costante.
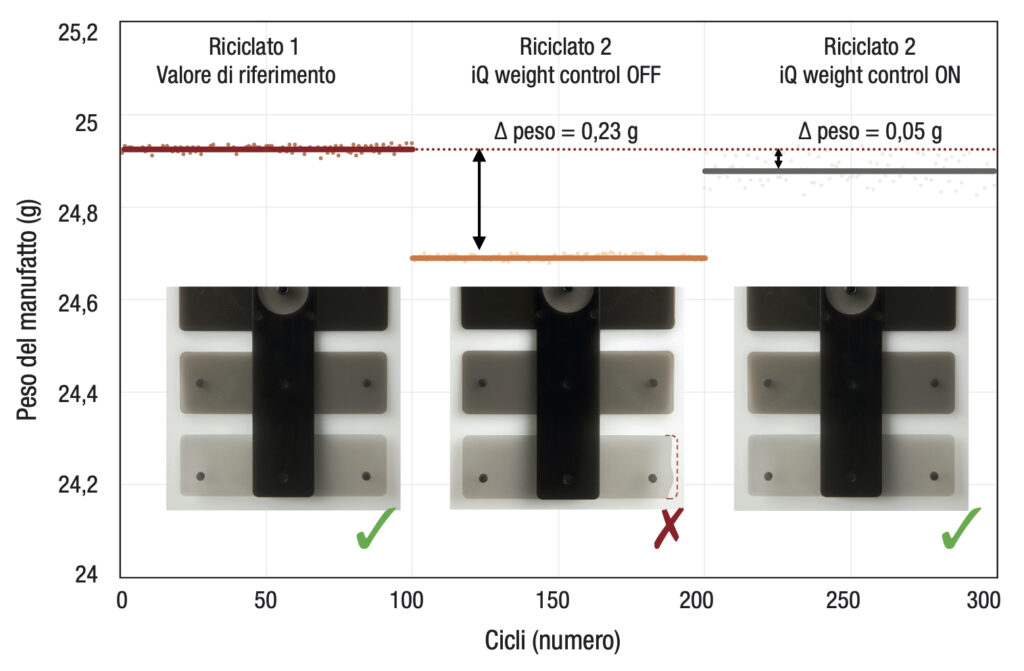
Il risultato è stato confermato anche dall’analisi delle curve di pressione rilevate all’interno dell’impronta (figura 4). In questo caso è stato effettuato anche il controllo tramite il trasduttore di pressione di iniezione integrato nella pressa. In fase di riempimento, si è osservato che la pressione richiesta cresceva sensibilmente nel caso del riciclato 2, caratterizzato da una fluidità inferiore. Con iQ weight control, il punto di commutazione, segnalato dalla linea verticale, e il livello della pressione di mantenimento sono stati regolati adeguatamente (figura 4, in alto).
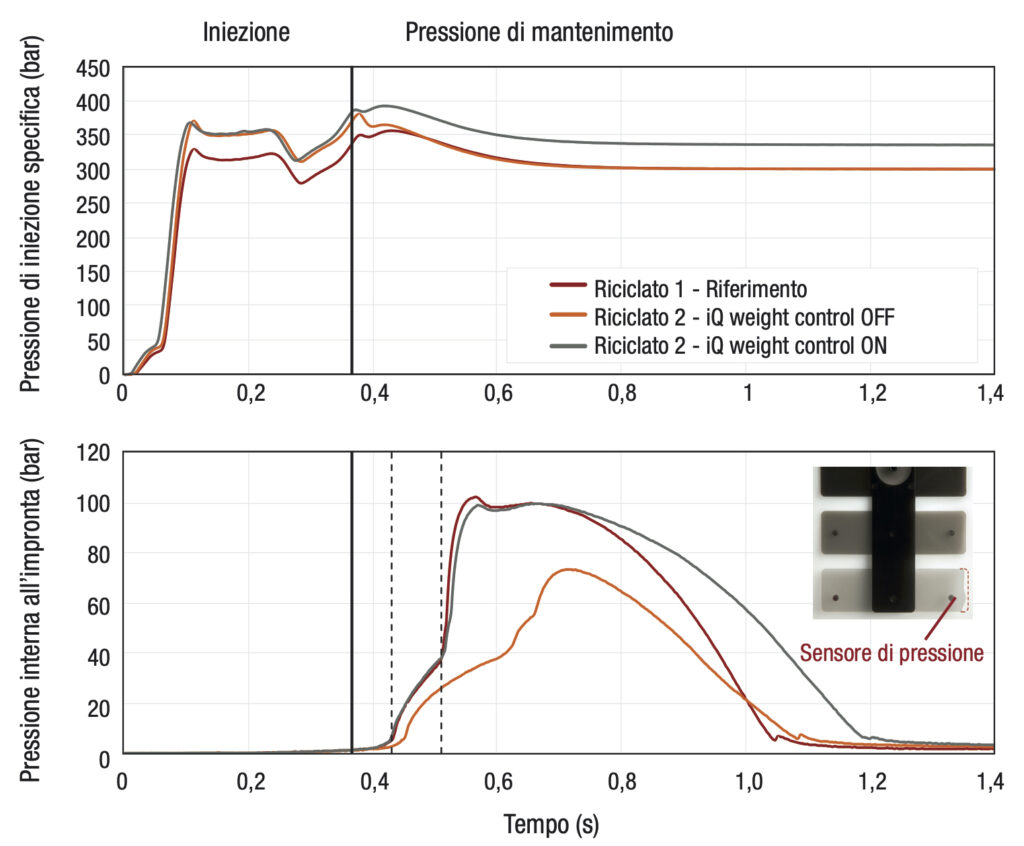
Analizzando il grafico è possibile notare due aumenti significativi (evidenziati dalle linee tratteggiate) lungo la curva di pressione rilevata all’interno dell’impronta. Il primo incremento di pressione si verifica nel momento in cui il fronte del flusso raggiunge il sensore di pressione all’interno dell’impronta, mentre il secondo corrisponde al completo riempimento dell’impronta oppure all’arresto precoce del fronte del flusso in caso di riempimento incompleto. Operando senza l’ausilio di iQ weight control si è osservato che il riempimento richiedeva tempi più lunghi, il che si traduce in un ritardo nell’incremento della pressione nello stampo, in una pressione sensibilmente inferiore nella fase di mantenimento e, in ultima analisi, in un riempimento incompleto dell’impronta. Con iQ weight control, invece, grazie all’adeguamento del punto di commutazione e del livello di pressione di mantenimento, la curva della pressione interna all’impronta risultava pressoché identica a quella rilevata durante la lavorazione del materiale di riferimento (figura 4, in basso