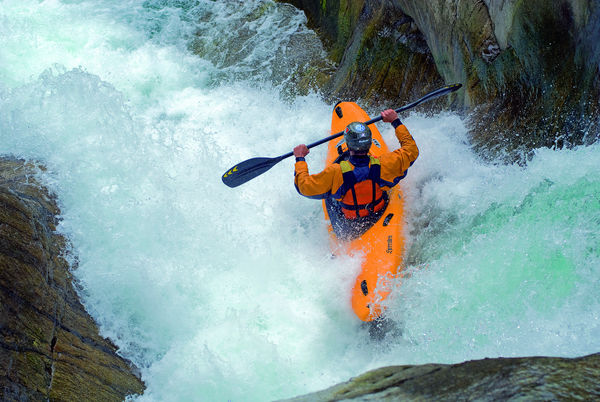
Il monitoraggio della pressione della cavità dello stampo migliora l’affidabilità di controllo dei processi di stampaggio a trasferimento di resina. L’obiettivo? Portare la tecnologia su vasta scala
La riduzione dei consumi di carburante, così come delle emissioni inquinanti, è diventata uno dei principali obiettivi dell’industria della mobilità. Raggiungerlo significa costruire veicoli sempre più leggeri. E in questo ambito, le materie plastiche rinforzate con fibre, in virtù dell’elevata resistenza e rigidità per unità di peso, si stanno ritagliando spazi di applicazione sempre più ampi. Tuttavia, i metodi di lavorazione dei compositi, come lo stampaggio a trasferimento di resina (resin transfer moulding o RTM), non sono finora riusciti a garantire una produzione industriale su larga scala.
La tecnologia dei sensori di pressione nella cavità dello stampo, già ampiamente impiegata nello stampaggio a iniezione tradizionale, potrebbe proporsi come un valido supporto nell’ottimizzazione del controllo dei processi RTM, permettendo così una maggior diffusione dei compositi in molti comparti dove la leggerezza è un requisito fondamentale: automotive, aerospaziale, sport e tempo libero.
La tecnologia RTM
Le tecnologie più adeguate alla produzione di strutture in plastica rinforzate con le fibre lunghe sono:
• laminazione manuale, per piccoli lotti e minimi requisiti di qualità;
• stampaggio per infusione di resina per il supporto di componenti strutturali di alta qualità, ideale per lotti di medie dimensioni (per esempio stampaggio a trasferimento di resina, RTM);
• processo di preformatura in autoclave, per componenti strutturali e applicazioni speciali (in particolare per le costruzioni aerospaziali).
Le criticità del processo di lavorazione delle preforme e i costi elevati in termini di investimenti e di energia per il processo in autoclave, hanno portato a preferire i metodi di lavorazione più semplici come, per esempio, lo stampaggio a trasferimento della resina (RTM), dal momento che quest’ultimo garantisce la stessa qualità della lavorazione delle preforme. Il metodo RTM viene impiegato soprattutto per le applicazioni hi-tech prodotte su larga scala, da 1.000 a 10.000 unità all’anno.
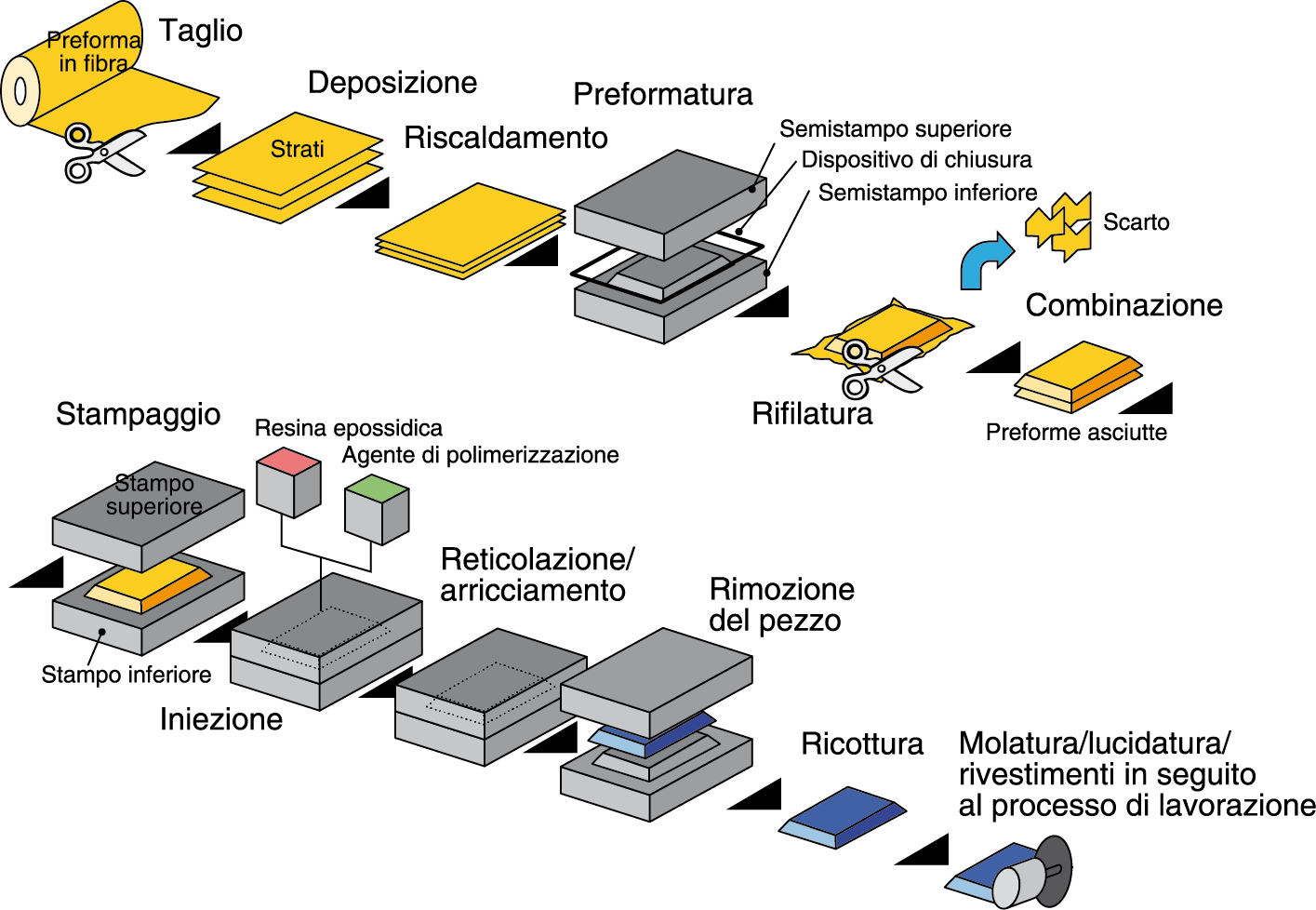
Nella figura 1 è illustrata la tecnologia RTM. La prima fase del processo è la termoformatura di fogli in materiale composito asciutti, un’operazione attraverso la quale vengono prodotte le preforme. In alternativa, queste ultime possono essere realizzate mediante intrecciatura, giunzione e cucitura. Una volta inserite le fibre rinforzanti in un doppio stampo, una resina termoindurente reattiva (generalmente un sistema epossidico) viene iniettata nello stampo. Grazie alla sua bassa viscosità, la resina penetra e bagna le fibre sottoposte a pressione. In seguito alla fase di iniezione, il manufatto subisce un processo di polimerizzazione con una reazione esotermica, dopodiché può essere rimosso dallo stampo.
Un controllo di processo efficiente richiede uno stampo e una tecnologia di sensori adeguati, due aspetti finora non disponibili insieme, come prodotto completo. Questo è uno dei motivi per cui il processo RTM non si è imposto nella produzione industriale su larga scala.
La simulazione del processo
La progettazione del pezzo e lo sviluppo del prodotto richiedono una selezione accurata del materiale – le preforme in fibra e le resine – oltre a uno studio di fattibilità del processo produttivo. Una parte essenziale di tale studio è la simulazione delle operazioni di riempimento dello stampo, allo scopo di verificare che il riempimento sia adeguato e che l’operazione avvenga entro un certo periodo di tempo, garantendo il livello di affidabilità richiesto.
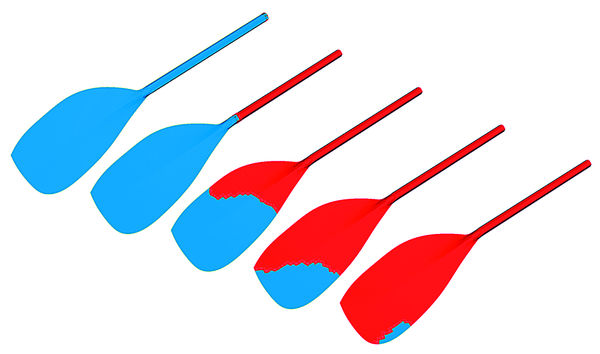
A titolo di esempio, la simulazione del riempimento di una pagaia (figura 2) evidenzia che la cavità dello stampo può essere riempita correttamente. Scegliendo in modo opportuno la strategia di iniezione è possibile evitare la formazione di soffiature.
I parametri più importanti
Dal momento che il processo RTM avviene all’interno di uno stampo chiuso, può essere controllato attraverso sensori inseriti nello stampo. Il processo può essere suddiviso in tre fasi principali:
• inserimento/riscaldamento della preforma asciutta;
• impregnazione delle fibre durante il riempimento dello stampo;
• polimerizzazione della resina mediante reticolazione chimica.
I parametri di processo che svolgono una funzione decisiva sono temperatura, pressione, viscosità e grado di polimerizzazione della resina. Tali parametri permettono di ricavare molte informazioni sul processo. Per esempio, la curva della temperatura fornisce informazioni sul riscaldamento della preforma asciutta, il passaggio del fronte di flusso della resina e la reazione di reticolazione chimica esotermica. La curva della pressione dà informazioni sul passaggio del flusso di resina attraverso il punto di misurazione e la distribuzione della pressione all’interno dello stampo. La viscosità fornisce indicazioni sulla fluidificazione della resina, mentre il grado di polimerizzazione sull’andamento della reazione di reticolazione chimica.
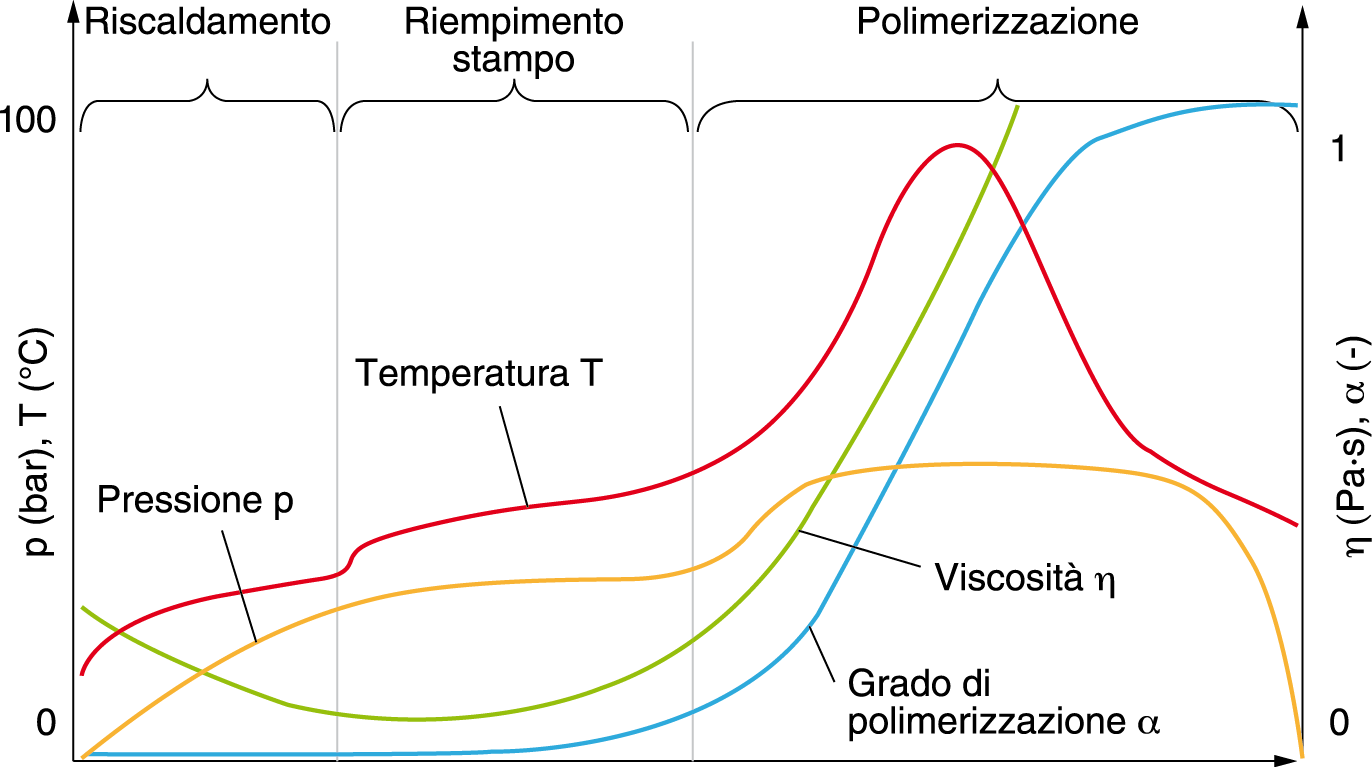
Come illustrato nella figura 3, i parametri di processo sopra elencati cambiano in funzione del tempo. Il grado di polimerizzazione viene dedotto da temperatura e viscosità (figura 4).
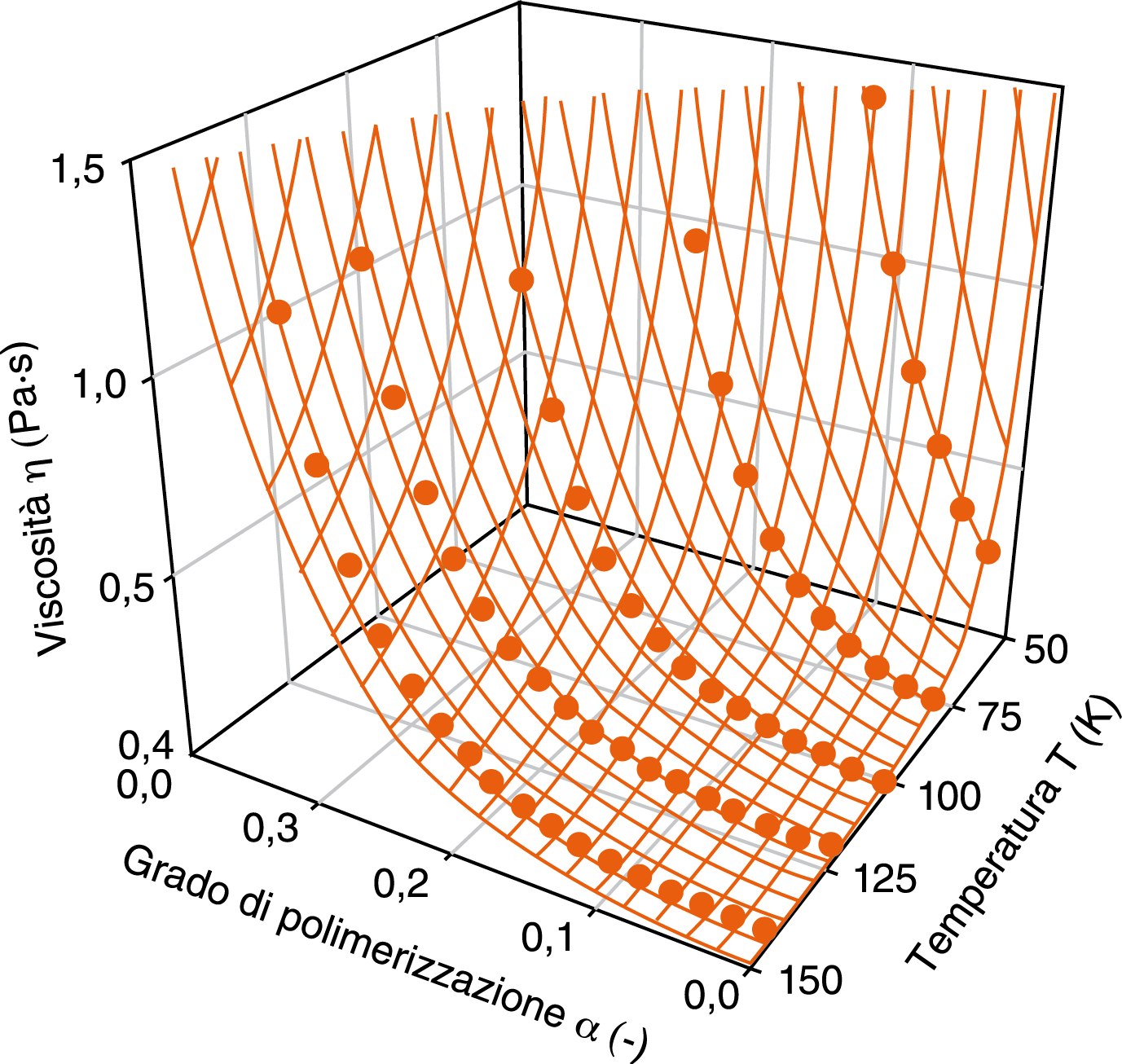
I parametri di processo influiscono sul processo di iniezione nonché sulla polimerizzazione della resina (figura 5).
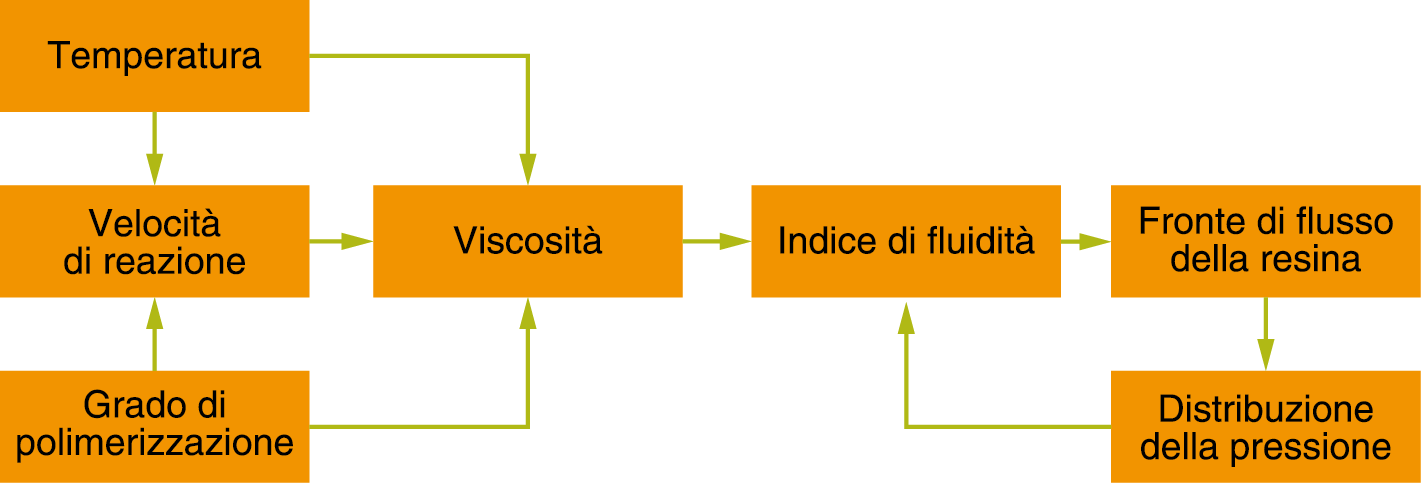
Il trasferimento di calore tra lo stampo, la preforma in fibra e la resina determina la curva della temperatura. La temperatura e il grado di polimerizzazione della resina definiscono la viscosità, il passaggio della resina attraverso la preforma in fibra e la velocità di reazione.
Controllo di processo con i sensori
Una tecnologia di sensori intelligenti e accuratamente regolati consente di registrare i dati di processo direttamente dai punti strategici all’interno dello stampo, fornendo informazioni precise nel corso del processo. In particolare, i segnali inviati dal sensore forniscono informazioni relative alla posizione del fronte di flusso, che possono essere impiegate per verificare se il fronte di flusso della resina ha già raggiunto il sensore situato in corrispondenza del punto di controllo. Il passaggio del fronte di flusso della resina contribuisce a determinare l’affidabilità del controllo di processo.
Altro punto importante, i dati di processo consentono di convalidare i risultati della simulazione. Inoltre, la sinergia tra le simulazioni numeriche e le informazioni di processo in tempo reale permettono di intervenire nel processo per migliorare i risultati.
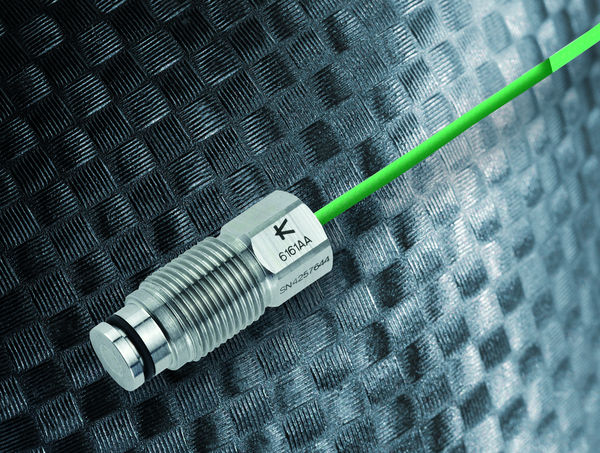
Il sensore di pressione 6161AA… di Kistler (figura 6) è ottimizzato per soddisfare gli speciali requisiti dei processi RTM. L’apparecchiatura è estremamente sensibile, tanto che è in grado di rilevare efficacemente le più piccole variazioni di pressione e le irregolarità nella curva della pressione durante il riempimento dello stampo. La curva della pressione registrata è molto utile per la documentazione del processo: infatti, la regolazione della pressione di iniezione fa sì che lo stampo venga riempito correttamente. In caso di stampi voluminosi, i segnali dei diversi sensori situati sul punto di iniezione facilitano il controllo strategico degli ugelli di iniezione.
Dotato di una tenuta o-ring, il sensore può essere utilizzato anche dopo l’evacuazione dell’impronta e per la misurazione del vuoto. L’applicazione del vuoto all’impronta agevola la fase di iniezione del composito resina/polimerizzante, eliminando soffiature all’interno del componente. La tenuta impedisce inoltre alla resina di penetrare nel foro di alloggiamento, facilitando le operazioni di montaggio e smontaggio del sensore.